PRES-X improves Laser Powder-Bed Fusion additive manufacturing with CANUNDA-HP Custom Shaper
PRES-X, Italy
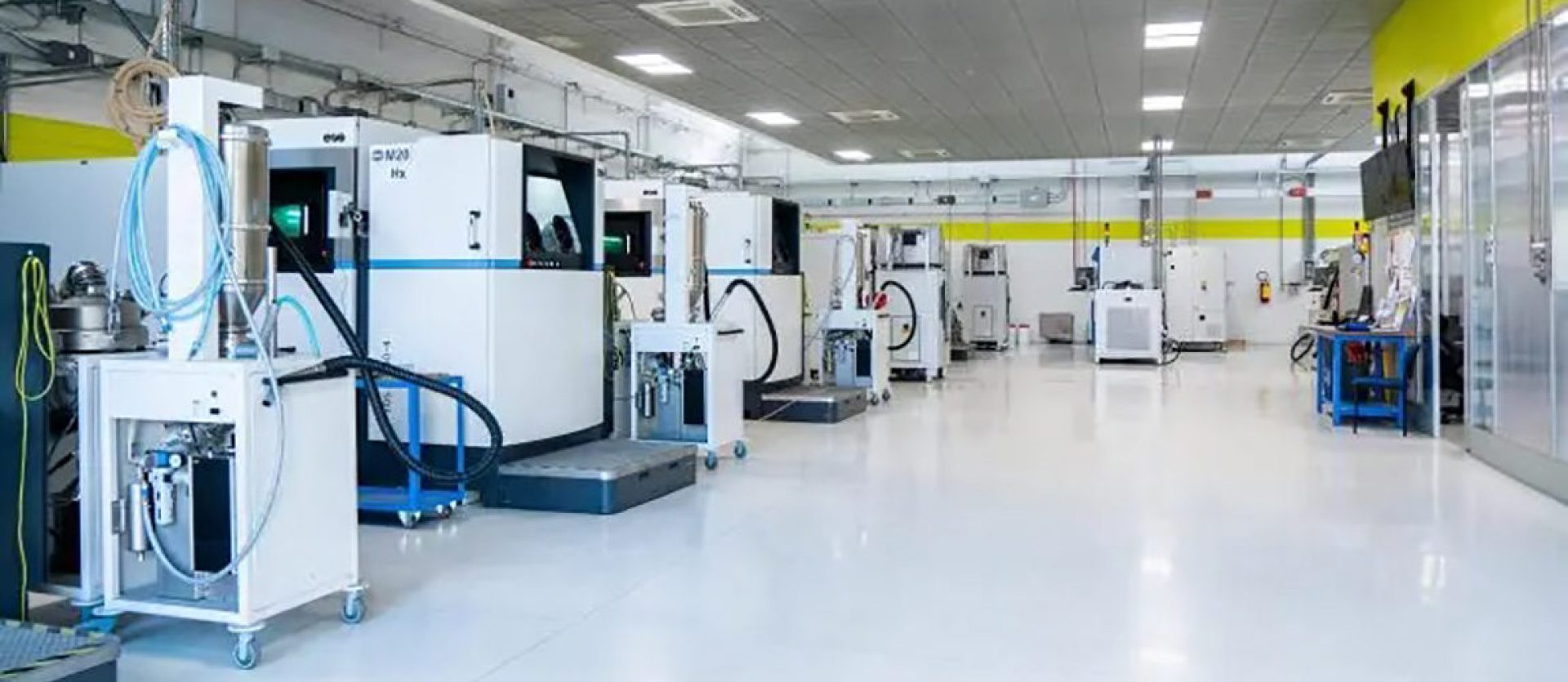
Laser Powder Bed Fusion (LPBF)…
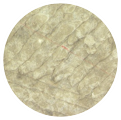
> Inconel 939
> 1030 nm
> 200 W
> 550-920 mm/s
> 99.9% density
… with a round top-hat
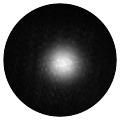
in the processing plane:
> Diameter : 90 µm
> “Multi-static » module
> Transmission >92%
Printable Material +1
The partner
PRES-X is an Italian additive manufacturing company specializing in post-processing solutions. Its parent company, BEAMIT, aims to produce high-end additive manufacturing metal components for the industrial sector and, to this end, has formed a global AM hub, offering a fully integrated value chain.
The application
Laser Powder Bed Fusion, or LPBF, is an additive manufacturing process. A high-power continuous-wave laser scans a specific path on a bed of metal powder, melting the metal as it passes. This allows parts to be printed in successive layers.
The problem
LPBF faces two major challenges. First, increasing process productivity is an essential precondition for mass producing parts rapidly. Second, the possibility of printing new materials would improve process flexibility.
The CANUNDA-HP Custom Shaper solution
The CANUNDA-HP Custom Shaper modules are used for custom static or dynamic high-power continuous-wave laser beam shaping. Based on Cailabs’ MPLC technology, its completely reflective design was conceived to handle very high-power lasers and can be adapted to all industrial environments.
“Beam shaping has significant potential for LPBF, and this is what we wanted to explore as part of the PULSATE AMLabs project. We were able to test different beam profiles in a very short period, and printed good quality Inconel 939 parts on an older generation machine that did not have this capability, so it was a success!”
Simone Barani, HIP Specialist, PRES-X
Industrial integration of CANUNDA-HP Custom Shaper
The CANUNDA-HP Custom Shaper multi-static module was installed on an additive manufacturing machine at PRES-X’s premises, and the reduced cracking during solidification enabled parts to be manufactured in Inconel 939, a Nickel alloy that previously could not be used with this machine.
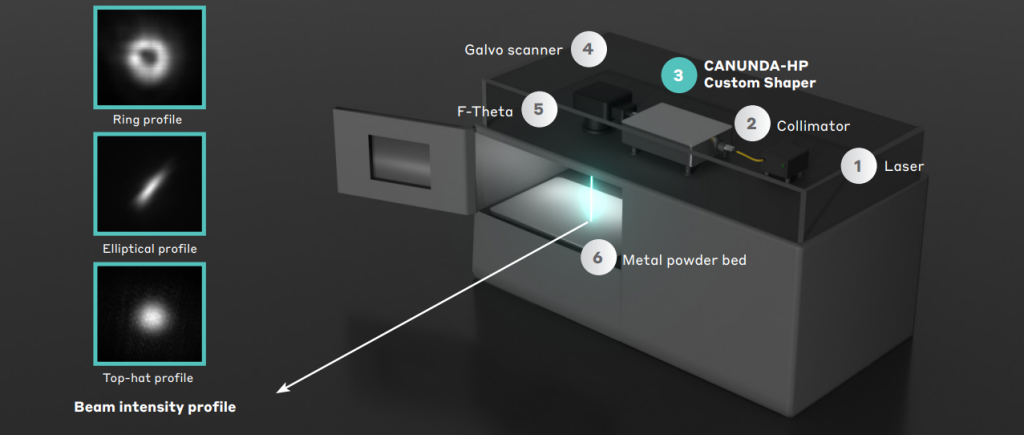
CANUNDA-HP Custom Shaper enabled the generation of three different beam shapes: a ring profile with an average diameter of 150 µm and a full width at half maximum (FWHM) of 70 µm; an elliptical profile of 90 µm x 280 µm @1/e² and a round top-hat profile with a diameter of 90 µm @1/e². The best results were obtained using the round top-hat beam profile: a wider process window, superior microstructure and mechanical properties.
Our Other Additive Manufacturing Case Studies:
-
CANUNDA-AXICON generates nanoscale surface structuring using a Bessel beam
-
Amplitude improves the ablation efficiency onto Aluminum with CANUNDA-PULSE (micro-drilling)
-
LASEA optimizes its femtosecond laser microfluidic chip welding processes with CANUNDA-PULSE
-
ALPhANOV increases surface texturing process throughput with CANUNDA-PULSE
-
Light Conversion and Cailabs demonstrate the compatibility of the CARBIDE laser with the CANUNDA-PULSE beam shaper