Why should you choose the MPLC for your laser beam welding process?
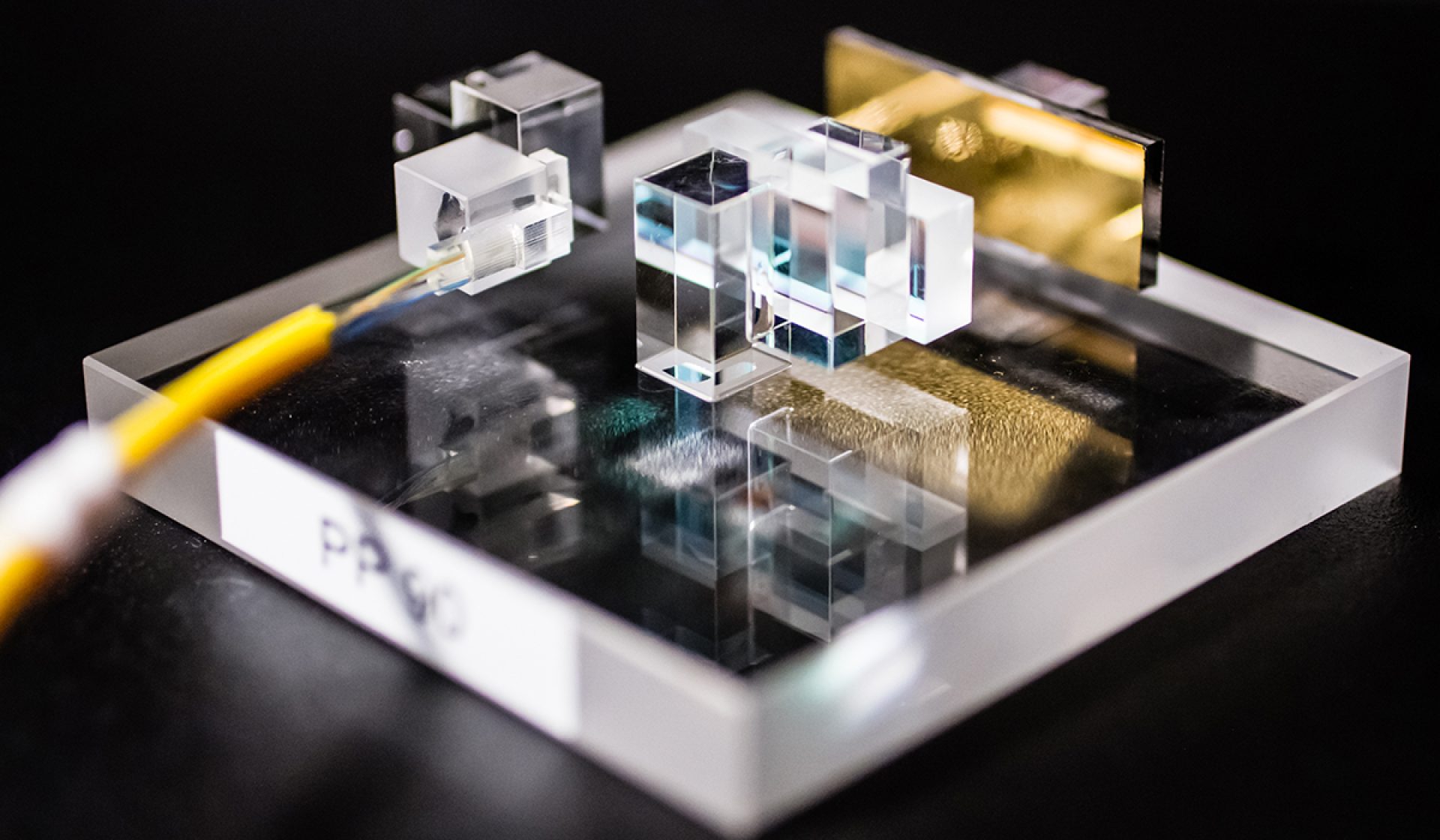
After having looked at the various conventional welding methods, we introduced the advantages of beam shaping for the laser process in the previous article. So, what are these various techniques, and what can they really achieve? Given the high power involved, why choose a reflective technology like the one developed by Cailabs?
Nb : this article is the third in a series dedicated to laser welding processes.
What are the selection criteria?
Common defects in laser welding are spatter, porosity, melt pool collapse and cracks. A good weld is primarily characterized by the absence of these types of defects. In general, the aim is to achieve a smooth weld bead with an even width. Therefore, choosing the right beam shaping technology will improve weld quality.
It is also important to implement a robust, reproducible process, i.e. one that will remain stable throughout its use, despite changing external conditions. For example, in laser welding, the large amounts of energy cause the beam-transmitting optics to heat up, which can create a temperature gradient along the surface of the optical element. This modifies the optical properties differently at each point on the lens, resulting in beam focus shift in the working plane. The aim is therefore to avoid this phenomenon, or at least to minimize its impact.
What beam shapes are used?
In laser welding, various energy distribution profiles are required, depending on the type of application and the materials to be joined. When welding steel, a ring beam shape is often used. This shape widens the keyhole opening, increases the width-to-depth ratio, limits spatter and increases process stability.(1)
For other materials such as copper or aluminum, a central spot surrounded by a ring is used. This ensures sufficient penetration, while the ring enables better temperature distribution.(2)
What technologies can create these shapes?
Double Core Fiber Lasers
The principle of this technology is relatively simple: the beam is guided through several concentric optical fibers (usually 2). Depending on the chosen configuration, the energy can be distributed either in the rings or in the center, so the shape of the beam changes.
Two separate laser resonators modulate the energy distributed between the two cores(1). This technology can form various beam shapes:
- A ring shape, sometimes called a “donut”,
- A central circular spot,
- A central spot surrounded by a ring, with several power levels.
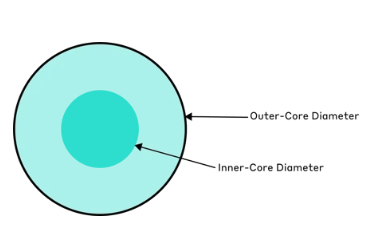
Diffractive Optical Elements (DOE)
Diffractive Optical Elements (DOE) use light diffraction to control the phase of the laser beam. Their microstructure pattern can be used to create any type of shape in a given plane. Depending on the wavelength of the beam used, they can be made of a variety of materials, such as plastics, fused silica, germanium, sapphire, or zinc selenide.
This type of element is wavelength sensitive, so it is designed for a specific laser.(3) It is also sensitive to alignment with the input beam and therefore requires frequent position adjustments.
Space Light Modulator (SLM)
Space Light Modulators (SLM) are optical devices that can manipulate the properties of light, such as amplitude, phase and polarization. They comprise a matrix of electronically controlled liquid crystals and can therefore generate a wide range of beam shapes “on demand”.(4)
Like a television screen, the resolution of the beam is limited by the number of pixels that make up the matrix. In general, they have difficulty handling high-power continuous-wave lasers, which means they are not very suitable for industrial applications. However, they are still very popular in research due to their beam shaping flexibility.
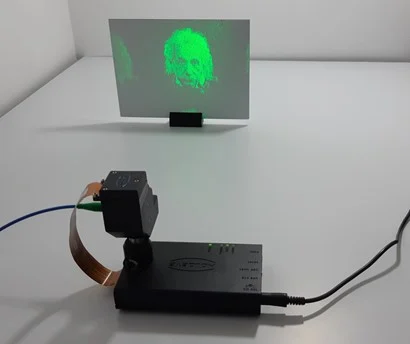
© 2020 HOLOEYE Photonics AG
Multi-Plane Light Conversion (MPLC): CANUNDA-HP Ring Shaper
The CANUNDA-HP module uses Cailabs’ patented beam shaping technology: Multi-Plane Light Conversion (MPLC). It is based on a succession of transverse phase profiles, similar to highly complex lenses, separated by a specific propagation distance.
So, the all-reflective design of the CANUNDA-HP means it can handle very high-power lasers, with homogeneous cooling. The module is designed for industrial environments, connected to fiber lasers.
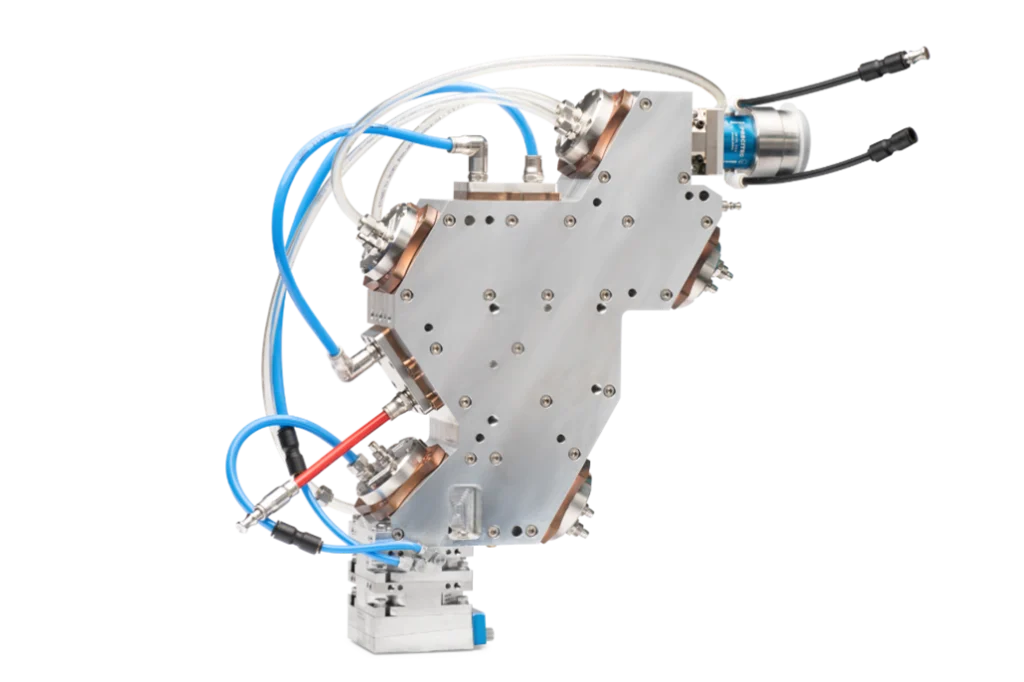
The standard configuration – the CANUNDA HP Ring Shaper – generates a ring with an inner diameter of 600 µm and an outer diameter of 1 mm. However, it can also generate any type of symmetrical or asymmetrical shape on request. In the next article, which concludes this series on laser welding, will focus on the module’s ability to operate outside its design operating conditions.
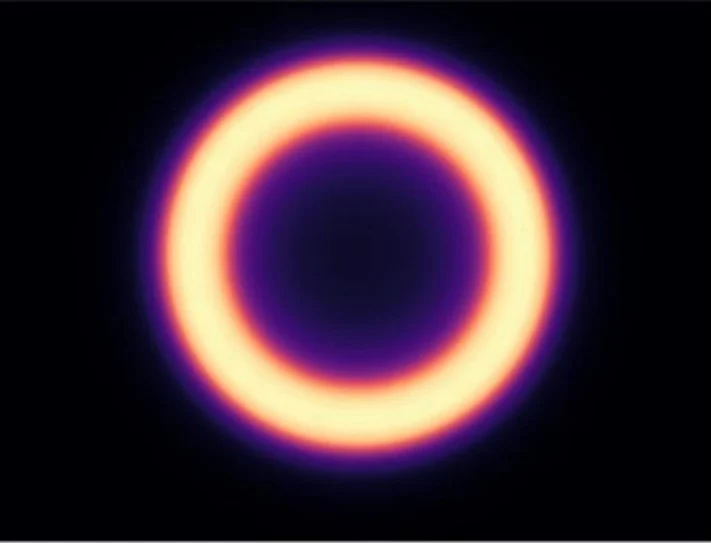
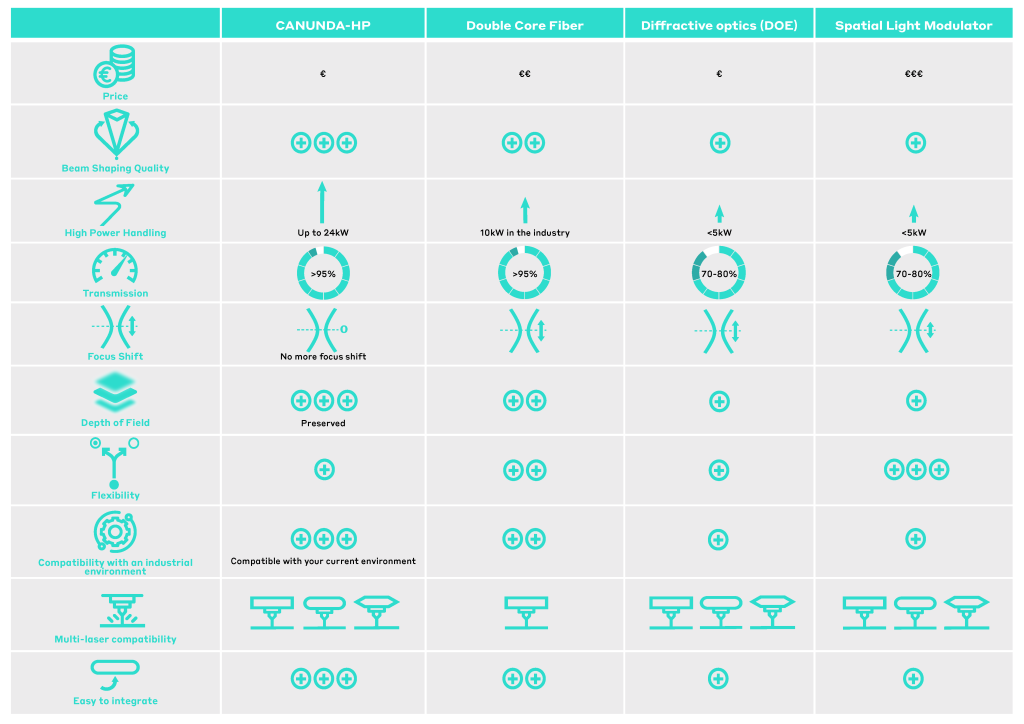
This table compares all the beam shaping technologies presented in this article, regarding 10 criteria. These latter are essential to implement a robust, reliable, and good quality laser beam welding process suitable for the industry.
For more information:
- The Cailabs’ Multi-Plane Light Conversion (MPLC)
- Publication technique | Freeform beam shaping with Multi-Plane Light Conversion for 1.07 µm ultra-high throughput laser-based material macroprocessing
- Technical publication | Fully reflective annular laser beam shaping for 1.03 µm ultra-high throughput laser beam welding
References :
(1) Adjustable ring mode and single beam fiber lasers: A performance comparison – ScienceDirect. Read the article
(2) High surface quality welding of aluminum using adjustable ring-mode fiber laser – ScienceDirect. Read the article
(3) Diffractive Optical Elements | DOE Optics | Edmund Optics For more information
(4) Spatial light modulator – Wikipedia. Read the article
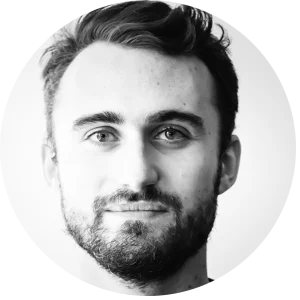
By Julien Bayol
Julien Bayol holds a Master’s degree in mechanics from INSA and has completed a Master’s degree in Management at Toulouse Business School. Very interested in advanced manufacturing techniques, through the use of innovative optical solutions, Julien is assistant product manager at Cailabs. He contributes to the development and commercialization of CANUNDA and TILBA® products.