Copper Welding
Transform Challenging Processes into Forgiving ones
By perfecting laser copper welding, we can achieve high-quality welds with minimal pores and spatter. Thanks to 1.5x process window and extended depth of field (4x) compared to dual core fiber, we guarantee shorter set-up times, lower scrap rates and improved reproducibility.
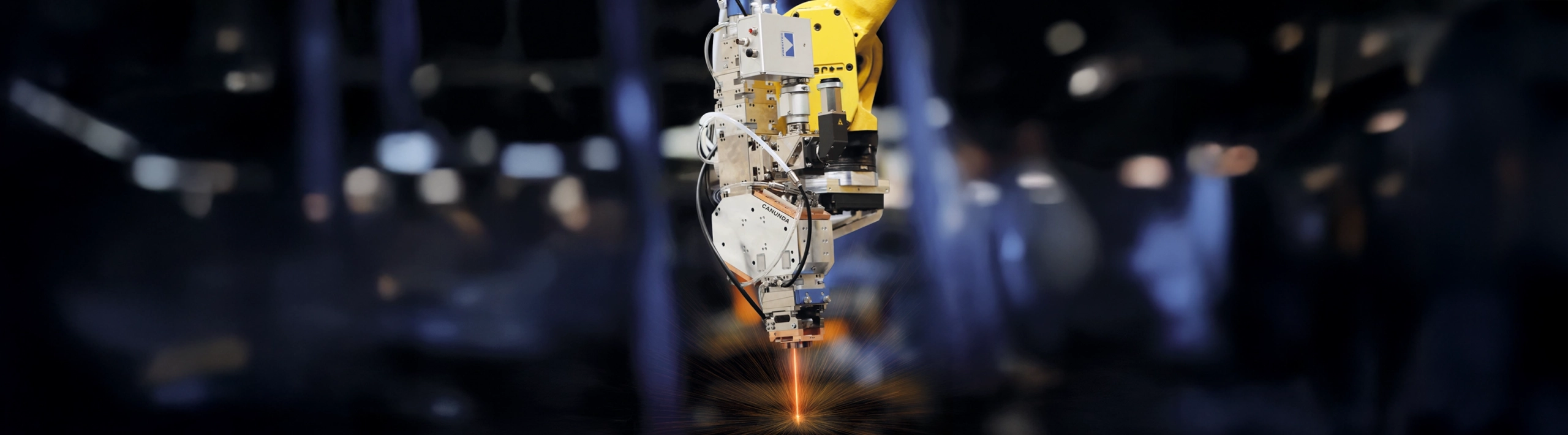
CANUNDA-HP for Copper Welding
Copper laser welding is a welding process that uses a concentrated laser beam to melt and fuse copper surfaces. Welding copper is challenging due to its high reflectivity at 1 µm – the wavelength of conventional infrared lasers. Moreover, it’s high thermal conductivity makes welding unstable, leading to potential defects such as: porosity, spatter and cracks.
By producing reliably high-quality welds for busbars and hairpins we are driving innovation in battery manufacturing and electrical power transmission.
The standard shaping head, CANUNDA-HP, emits a beam consisting of an intense spot surrounded by a ring. This configuration ensures industrial-quality welds by minimizing pores and spatter and ensuring good penetration depth.
The fully reflective design of our modules, combined with optimal cooling from the rear of the optics, gives our products the robustness required to withstand the extreme power demands of copper welding.
However, we also offer customized, flexible solutions to suit a variety of copper welding requirements (new beam-shapes, different spot sizes, specific mechanical designs …). Each of our products is meticulously tailored to your industrial environment (scanner, robot arm …), offering seamless compatibility with all types of fiber lasers.
Industrial Integration of CANUNDA-HP
6-axis Robot
LLK-D Connector
Shaping Mirrors
Laser beam intensity profile at nozzle exit
Focusing Lens
Collimation Lens
Shaping Mirrors
Busbars Copper Laser Welding for E-mobility Applications
Customize your CANUNDA
Do you want to improve the performance of laser machining processes?
Contact us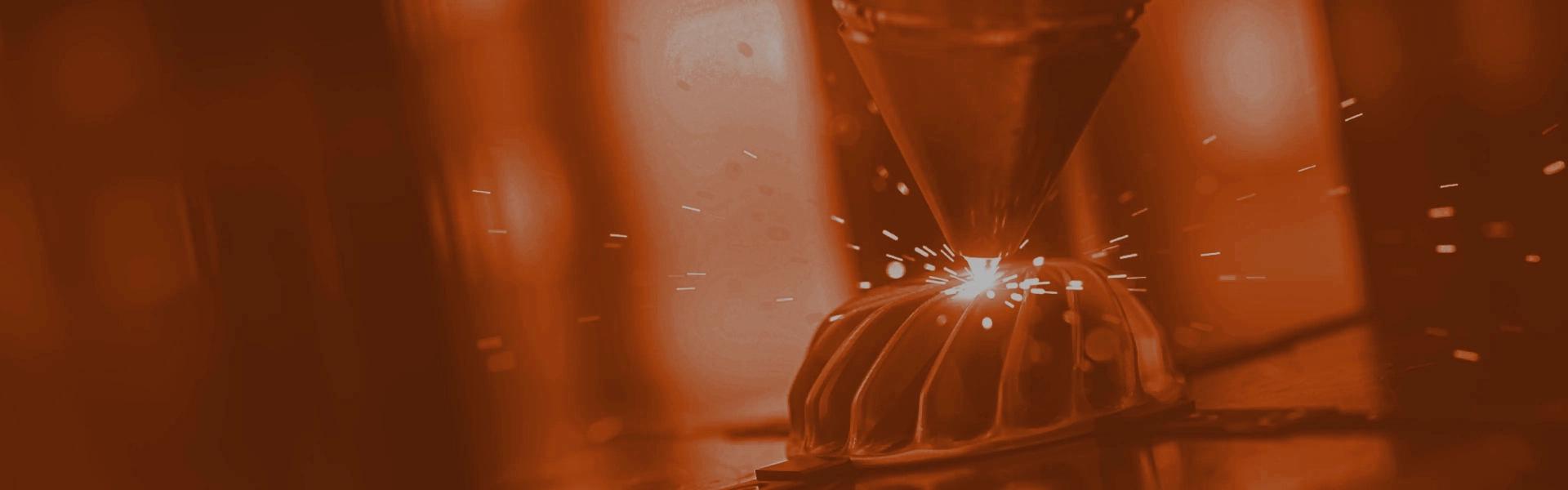