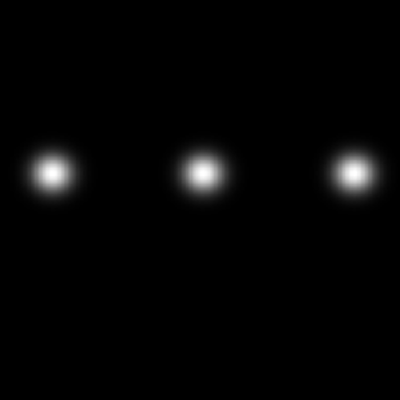
IFSW improves copper laser welding with CANUNDA-HP Custom head
IFSW, Germany (Copper welding)
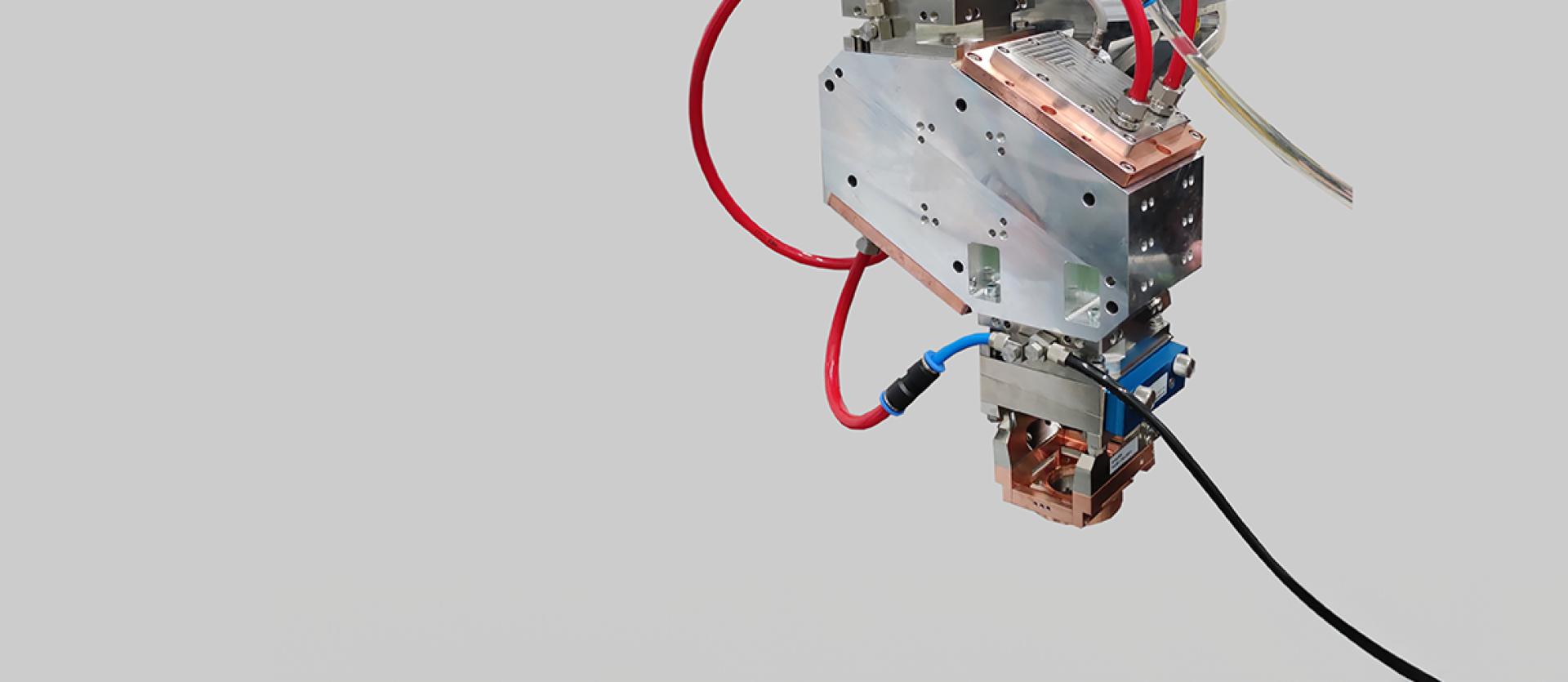
Copper Welding …
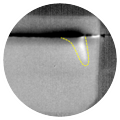
> CU ETP
> 1030 nm
> 8 kW
> Large depth of field (+/-4 mm)
> Process window: 3-35m/min
> Limited pores and spatters
… with a central spot and a ring
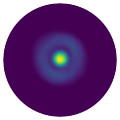
in the processing plane:
> Ø Dot = 125 µm
> Ø Ring = 500 µm
> 70% Spot, 30% Ring
Depth of Field x2
The partner
Founded in 1986, the Institut für Strahlwerkzeuge (IFSW) of the University of Stuttgart is reputed as one of the world’s leading laser research centers. Its research covers every aspect from laser sources and applications to fundamental research and industrial technology transfer. Currently, part of its research activity is focused on the use of beam shaping.
The application
One of the major challenges of e-mobility is copper welding. Many of the components required to operate batteries are made of copper and need to be welded together. For example, busbars are copper parts that must be welded for electricity to pass from one component to another (battery, motor, etc.).
The problem
FSW is looking for a custom beam shaping technology to ensure optimum-quality copper welds, without pores or spatter. It is also seeking to identify a robust industrial solution with the widest possible process window (speed/power range).
The CANUNDA-HP solution
The CANUNDA-HP Custom head delivers an intense spot beam surrounded by a ring, which is ideal for welding copper. Its fully reflective design based on Cailabs’ MPLC technology allows for optimal cooling of the optics, making it compatible with high power lasers.
Industrial integration of CANUNDA-HP Custom laser head
The CANUNDA-HP Custom head was used at IFSW to weld 100 mm x 30 mm x 4 mm Cu-ETP copper samples using argon shielding gas. A matrix of 3 x 7 tests (three power values and seven robot velocity values) was analyzed by live X-ray to determine the capillary length and visualize pore formation and spatter. An X-ray tube was positioned in front and a camera behind the sample.
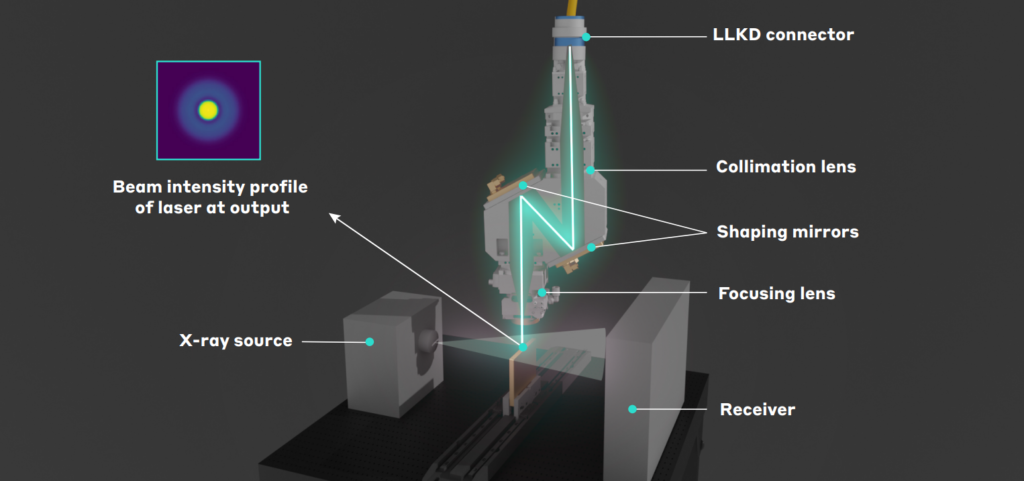
The CANUNDA-HP Custom laser head was configured to generate a 100 µm diameter spot surrounded by a 400 µm diameter ring (70% of power in the ring, 30% in the central spot).
“At IFSW, we are currently researching various laser technologies to improve copper welding, a major issue for e-mobility. Our X-ray analysis of the sample during the welding process showed that Cailabs’ solution demonstrated industry-compatible weld quality and bead stability.”.
Felix Zaiss, PhD student at IFSW