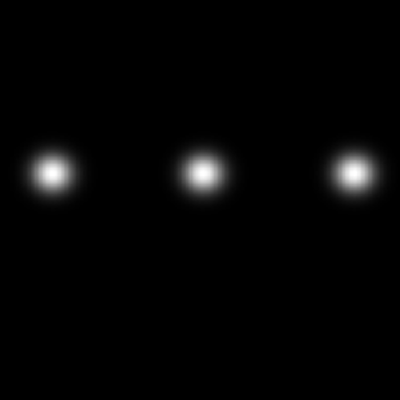
Institut Maupertuis improves copper laser welding with CANUNDA-HP Custom head
Institut Maupertuis, France (Soudage cuivre)
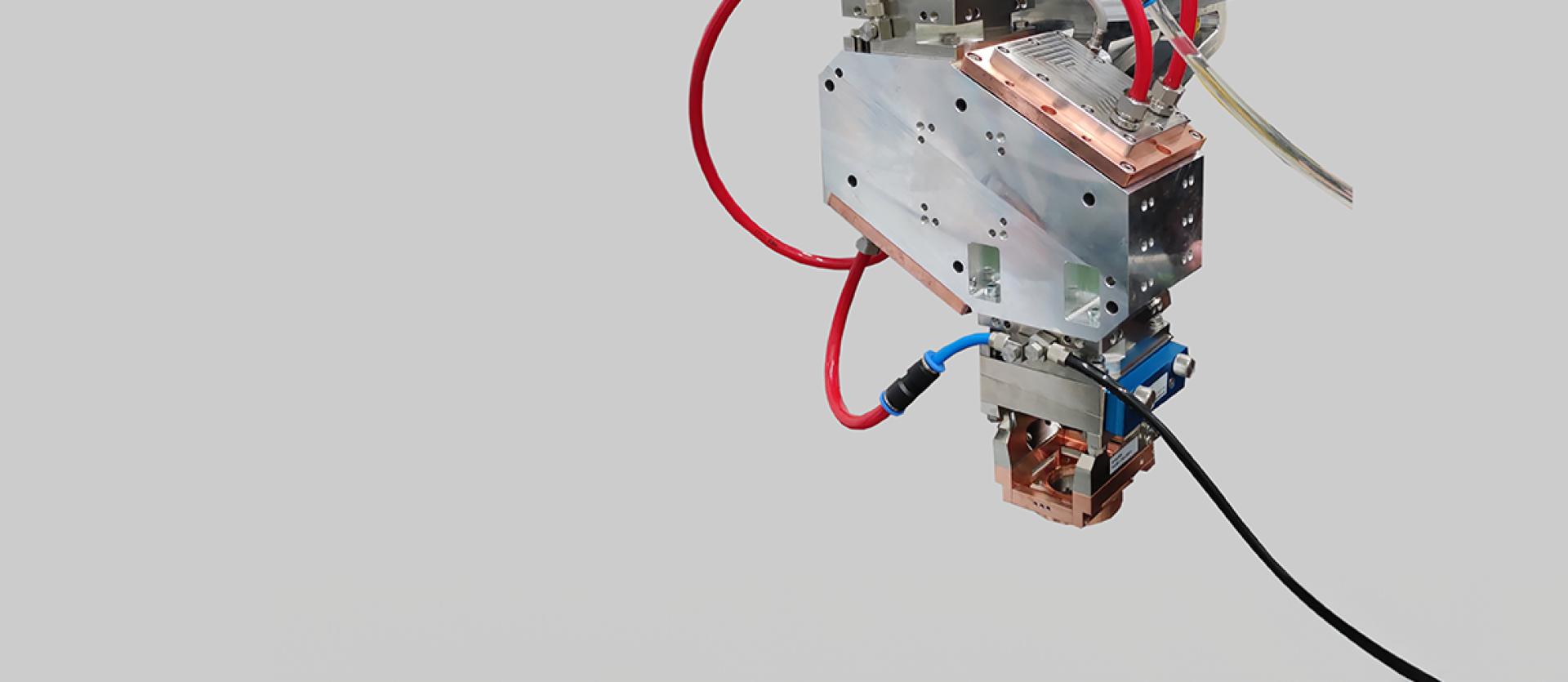
Copper Welding …
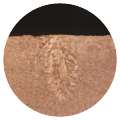
> CU ETP
> 1030 nm
> 8 kW
> Large depth of field (+/-4 mm)
> Process window: 3-15m/min
> Limited pores and spatters
… with a central spot and a ring
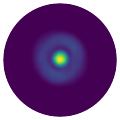
in the processing plane:
> Ø Dot = 125 µm
> Ø Ring = 500 µm
> 50% Spot, 50% Ring
Process Window x1.25
The partner
Institut Maupertuis, a French center of industrial expertise with a test platform and high-quality devices, specializes in high-power laser processes such as laser welding, laser cutting and additive manufacturing. The institute seeks to offer new solutions to the issues faced by its industrial partners.
The application
One of the major challenges of e-mobility is copper welding. Many of the components required to operate batteries are made of copper and need to be welded together. For example, busbars are copper parts that must be welded for electricity to pass from one component to another (battery, motor, etc.).
The problem
The Institut Maupertuis wants to identify a custom beam-shaping technology to ensure optimum-quality copper welds. The aim of the tests is to evaluate the optical configuration of the most suitable head from a process point of view, and to demonstrate the advantages of this solution over its competitors.
The CANUNDA-HP Custom solution
The CANUNDA-HP Custom head delivers an intense spot beam surrounded by a ring, which is ideal for welding copper. Its fully reflective design based on Cailabs’ MPLC technology with optimal cooling of the optics allows it to handle high laser power.
Industrial integration of CANUNDA-HP Custom laser head
The CANUNDA-HP Custom head was used at the Institut Maupertuis to weld 10 mm thick Cu-ETP copper samples using argon shielding gas. A 5×5 test matrix (five power values and five robot speed values) for each of the four optical configurations (see tables) was used to determine the optimum configuration. The criteria were weld bead stability and/or penetration. The head was tilted to prevent reflections from damaging the equipment.
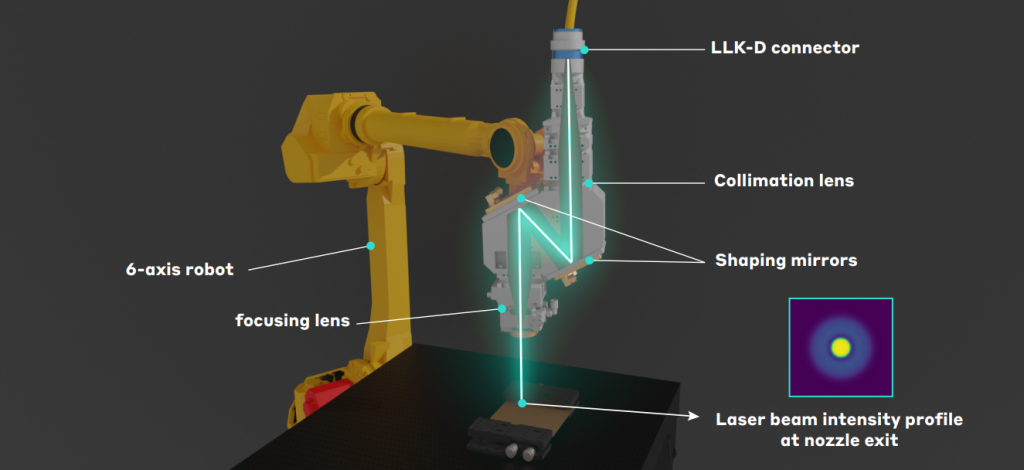
Of the 4 configurations tested, the best performing solution was the following: 50% in the central dot, Ø Dot = 125 µm, Ø Ring = 500 µm, collimator focal length = 200 mm, focus focal length = 250 mm, it is the only solution that gives 100% compliant weld beads for penetrations of between 0.4 mm and 2.8 mm.