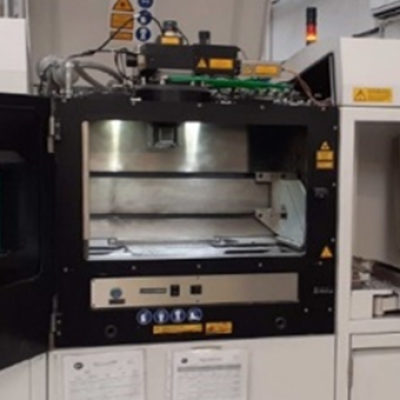
AIMEN improves welding processes with dynamic beam shaping using CANUNDA-HP Custom Shaper
AIMEN, Spain
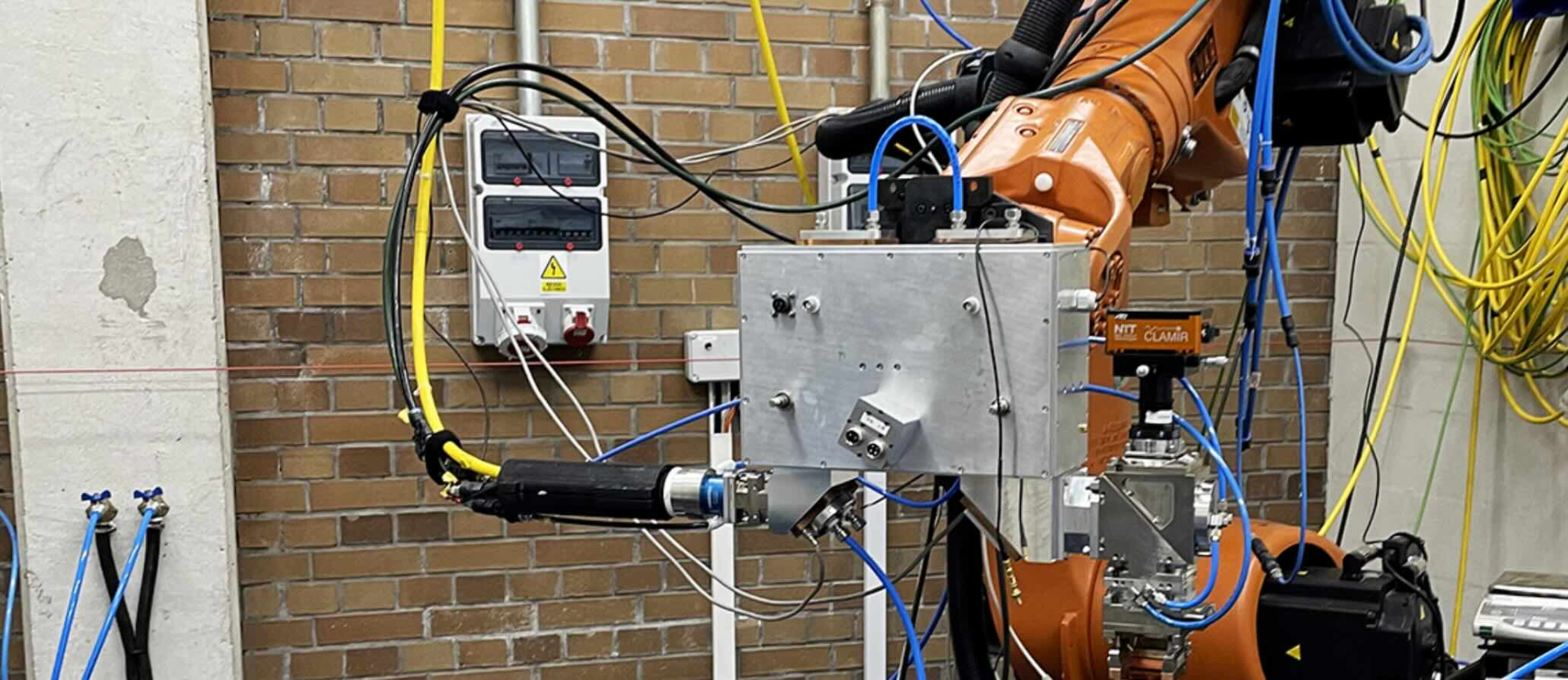
Stainless Steel Welding…
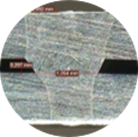
> 304L stainless steel
> 1030 nm
> 8 kW
> 80 mm/s
> 0 mm to 0.4 mm gap
…with dynamic rectangle & dot shape
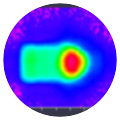
in the processing plane:
> Ø Dot = 0.7 mm
> Rectangle length: 1.6mm
> Adjustable rectangle width: 0.8 to 1.5mm
Gap managed x2
The partner
AIMEN is a Spanish innovation and technology center specialized in joining technologies and laser technologies applied to materials processing, robotics and automation. Through its research and development activities, the center aims to contribute to improving technological resources in this area.
The application
Laser welding consists of joining multiple, generally metal parts using a high-power laser. The heat generated melts the material to form a weld pool. As the weld pool cools, the parts fuse together.
The problem
One of the major challenges of standard laser welding processes in the automotive industry is assembling parts with a gap, especially interlocking tubular parts. Beam shaping can facilitate this task while maintaining quality and productivity levels.
The CANUNDA-HP solution
The CANUNDA-HP Custom Shaper laser heads are used for custom static or dynamic beam shaping of high-power continuous-wave lasers. Based on Cailabs’ MPLC technology, its completely reflective design was conceived to very handle high-power lasers and can be adapted to all industrial environments.
“The dynamic MPLC system developed by Cailabs has demonstrated its effectiveness in solving the quality problems that arise during the welding of vehicle exhaust system components with gap. […] Concerning hot fatigue testing, the MPLC solution provides much better results.”
Jorge Arias, AIMEN Technology Centre
Industrial integration of the CANUNDA-HP Custom Shaper
The CANUNDA-HP Custom Shaper laser head was integrated into a robot arm at AIMEN’s premises to perform gap welding of flat and tubular parts made of 304L stainless steel at a speed of 80 mm/s. With a gap ranging from 0 mm to 0.4 mm, welding with the CANUNDA-HP Custom Shaper met the quality requirements set by MARELLI, supplier of components for the automotive industry.
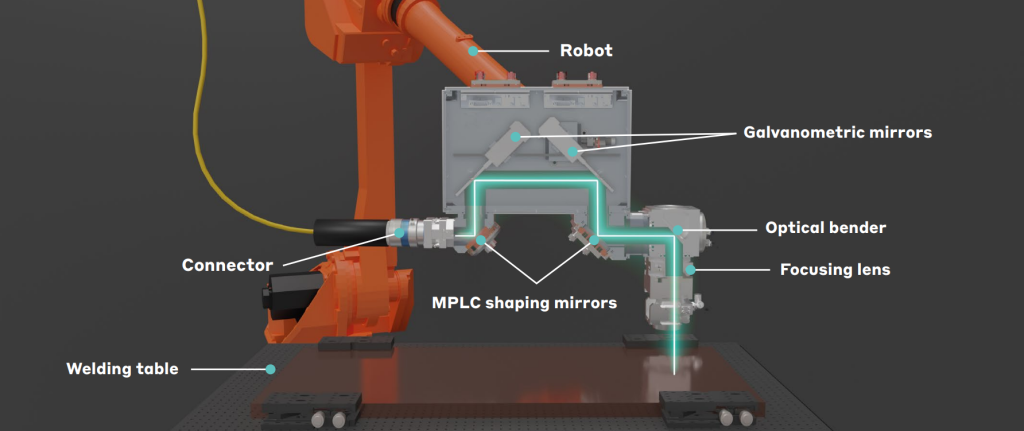
The CANUNDA-HP Custom Shaper laser head made it possible to generate a dynamic beam shape divided into two parts: a main spot of 0.7 mm diameter to create the weld pool, and a secondary rectangular beam of 1.5 mm in length and an adjustable width of between 0.75 and 1.77 mm, which allowed the temperature gradient to be controlled. The power ratio between the two beams can be adjusted via real time monitoring.